Horse whims
Aspen Times Weekly
Aspen, CO Colorado
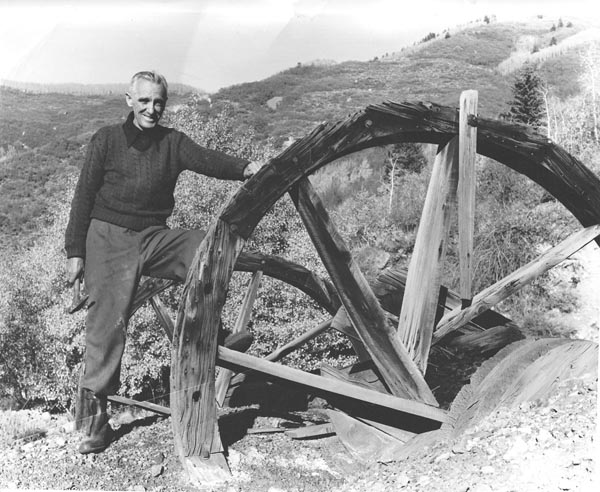
ALL |
Watching my neighbor lift his motor from his car reminded me of the challenges that miners faced when lifting material from the bottom of mine shafts. Raising heavy objects is difficult enough, even when a sturdy frame, like my neighbor’s, can be erected directly above the object to be lifted. Mechanical advantage comes into play with a series of pulleys driven by a powerful motor connected to a strong cable. Small mining operations’ loads were as heavy as a car engine, but miners did not have our modern conveyances. Additionally, they had to lift their loads longer distances.
Although most of early Aspen’s mine shafts were operated by small crews of miners, some were solo endeavors. Having little capital, men had to improvise methods of raising rock from below. Carrying a bucket of rock up a shaft ladder was both arduous and dangerous; one hand on a ladder is half as safe as two.
Some miners installed a simple, hand-cranked windlass that worked like those used to crank a bucket of water up from a well. A miner on the bottom level loaded a bucket that was attached by a rope to a spindle, sometimes nothing more than a tree trunk. Then a surface worker cranked a handle to wind the upper end of the rope around the spindle, drawing the bucket towards the surface. The only mechanical advantage would be afforded by the turning windlass cylinder and sometimes by the addition of a pulley positioned over the center of the shaft.
Author Will Meyerriecks, in his book “Drills and Mills: Precious Metal Mining and Milling Methods of the Frontier West,” estimated the capacity of the windlass to be four tons lifted in eight hours, using two men, from a depth of about 75 feet. Most windlasses used hemp rope that frayed and broke from use. A 100-foot shaft provided adequate infrastructure for a small mining operation or a short vein, but once a miner exceeded that depth, a windlass was worthless.
For shafts between 100 and 300 feet deep, a horse whim was an inexpensive solution. It was a simple device: a long arm, driven by a horse or mule that walked around in circles, was attached to a vertical drum for winding cable. The whim is an ancient device that was updated for mining purposes. Miners could fashion one from wood and a few metal parts or buy a manufactured, all-metal whim.
Meyerriecks figured the capacity of the whim to be 10 tons lifted in eight hours, using two men and a horse, from a depth of 200 feet. The whim provided more than double the capacity at twice the depth of a windlass. To give you some idea of the problem faced by those who extracted Aspen’s silver/lead ore, a ton would be about the size of a bale of hay. Ten tons required a minimum of 20 lifts. Lighter, unprofitable rock, given the same bucket size, would require many more lifts, about one every 15 minutes.
At one time you could find abandoned horse whims around Aspen. As the wooden parts rotted and hikers carried off the metal parts, the only remaining sign of a whim was the deeply-trodden circular paths worn by horses adjacent to the shaft openings. Over time, most of those were covered with vegetation or eroded beyond recognition. The only one I know that is still recognizable lies beside one of the few remaining open shafts in the Columbia Mining Lode above Ashcroft. Resting in the open basin above the Markley Hut, it is easy to find, providing a rewarding hike for anyone who is fascinated by the challenges miners faced moving rock from the depths of mountains.